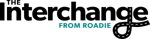
3 ways to prepare for last-mile success before spring construction season
The construction industry’s traditional winter lull can actually be one of the most exciting times for your business. With an eye toward cleaning up facilities, improving processes, and maximizing efficiencies, now’s the time to plan for maximizing your spring construction profitability.
Adding crowdsourced delivery to your last-mile logistics mix makes the process even easier. Here are three business areas where you can get the off-season ball rolling and start spring construction season with more momentum than ever before.
Get your warehouse under control
Misplaced tools, disorganized inventory, and uncoordinated staging are common but costly issues for construction industry businesses. Payment-processing company Levelset found that construction businesses lose more than one full day of work every week due to process inefficiencies. Other industry estimates suggest companies spend more than 30% of annual tool purchases on replacing lost, damaged, and stolen tools. On top of that, shrinkage can pinch the bottom line. LBM Journal suggests that 0.5% of sales is an acceptable shrinkage amount due to damage, loss or administrative error. That means $50,000 for every $10 million sold — no small figure.
To prevent this wasted time and money, take care of your warehouse during the off-season so you’re ready to roll when spring construction begins.
- Deep clean your warehouse by clearing clutter and trash, scrubbing and sanitizing workspaces, and replacing bulbs in overhead and task lighting.
- Inspect and repair all tools and heavy equipment. Create an inventory of what you have on-hand, and order replacement pieces to fill in any gaps.
- Add racking or better organize your existing vertical storage to keep materials safe from damage and easily accessible.
- Create processes for signing out tools, or implement new technologies to track tool use and whereabouts.
- Check safety and security measures to ensure your warehouse – and everything in it – is only accessible by approved personnel.
Identify efficiency improvements
With your warehouse and tools in tip-top shape, it’s time to turn your attention to processes that will keep your operation running smoothly and profitably all season. Getting materials into your warehouse and out to job sites efficiently is key, and leveraging crowdsourced delivery can help you maximize both time and money in a variety of ways.
Eliminate DIM weight and LTL fees
Warehouses that stock and move building materials are well aware of up-charges incurred for dimensional weight (DIM) application, or less-than-truckload (LTL) orders. With DIM weight, fragile items like light fixtures that require extra packaging, or oddly dimensioned materials like batt insulation can end up costing more to ship because of their large sizes. Specialty orders that don’t maximize the truck’s space, or shipments that are off your regular schedule of stock deliveries, can incur LTL fees.
Crowdsourcing with Roadie helps eliminate fees in both of these scenarios. The network’s wide variety of vehicle and driver capabilities means senders can move any product no matter the size, shape, or weight without incurring extra dim-weight fees or upcharges. Whether you’re moving materials from a distribution center to your warehouse, or between multiple warehouse locations, inventory redistribution is easier with crowdsourcing.
Smooth out your staging areas
Once materials are in the warehouse, take time to organize your staging area so the right materials – and only the right materials – head back out to each jobsite. Create bays where warehouse managers can organize all the materials needed for an individual project. This prevents crews from grabbing an extra case of caulk or a few sheets of plywood, and helps reduce shrinkage.
Better yet, use Roadie to distribute materials for you. Construction crews can head straight to their job sites, met there by a crowdsourced driver carrying exactly the materials they need to get started and keep going all day. This gives your warehouse team full control over what enters and leaves the facility, and maximizes your crews’ time on site without burning any daylight. Make the most of this approach by equipping your warehouse with clear signage and processes for working with delivery drivers when they arrive.
Keep your warehouse teams in the warehouse
Jobsite surprises are inherent in the construction industry. Whether a crewmember knocks over a bucket of paint, reveals unexpected termite damage, or simply forgets to measure twice, there will be instances where extra materials are needed right away. Running out of consumables like thinset or fasteners happens too. Rather than taking someone off the jobsite or out of the warehouse to run replacement materials to the crew, let a Roadie driver handle it for you. Enabling ultrafast, on-demand delivery is a Roadie last-mile specialty that will give your team members the most up-time possible.
Engage employees for growth
The off-season is an ideal time for you and your crews to cross off continuing education classes before work gets busy. Encourage your team to take classes to improve their skills, such as forklift operation or warehouse management. Also, consider hosting a supplier lunch-and-learn where your partners visit for on-site product training.
If you’ve spent the busy construction season telling yourself, “I really need to get that warehouse cleaned out,” or “I need to trim some unnecessary fees from the budget,” now’s the time. Tackling any or all of these spring readiness steps can make your construction off-season a highly productive part of your year, and the Roadie team is ready to help maximize your productivity gains. Check out all the ways Roadie can help you put crowdsourced delivery to work for your construction business today.
Beyond nuts and bolts: Crowdsourced delivery built for construction
Related Posts
Subscribe to our logistics newsletter
Get once monthly resources and insights into logistics challenges and trends. Add your email in the form to the right, or feel free to jump back into the site!