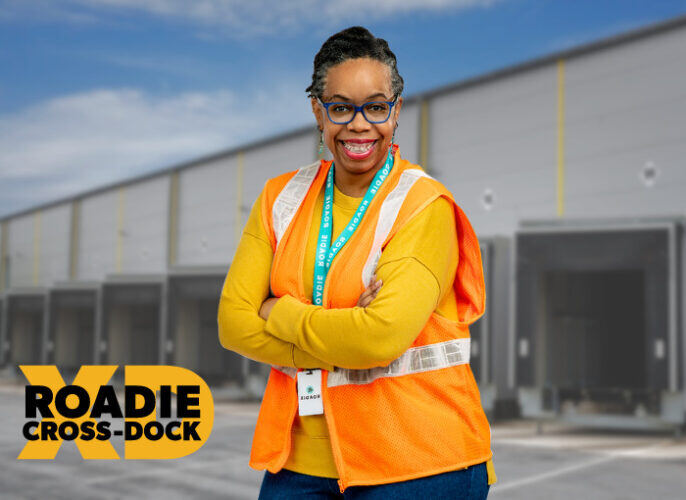
Speed is king when it comes to moving goods. When merchandise travels quickly through the supply chain, senders minimize inventory carrying, handling, and storage costs; customers get their orders faster; and suppliers cut their order-to-cash cycles. It’s a win-win-win.
Cross-docking has become a best practice for achieving these great benefits. A practice in which shippers sort and reload inbound inventory directly onto outgoing vehicles, cross-docking mitigates the need for long-term storage of goods. Often the next stop for cross-docked goods is the customer’s loading dock or front door.
The accelerating pace of the marketplace means cross-docking is booming, with a compound annual growth rate of about 6% through 2030. E-commerce is a big driver, but industries as varied as food and beverages, pharmaceuticals, automotive, paper and pulp, and defense and aerospace are increasingly leveraging cross-docking in their supply chains. Perishable goods often benefit from cross-docking to ensure they stay fresh and safe.
According to the annual 2024 Third-Party Logistics Study, 35% of shippers use an outsourcing partner for cross-docking. Of course, that also means that 65% of shippers don’t use cross-docking, even though many of them would likely benefit from the process. This statistic suggests that a majority of senders see limitations in the cross-docking options currently available to them.
Why should senders cross-dock?
Skipping the putaway, storage and picking aspects of the distribution process delivers many benefits. In addition to increasing shipping speed, cross-docking means reducing or eliminating the cost of storage space, lowering labor costs, and minimizing the potential for damaged goods by minimizing touches. It can also drive greater flexibility and scalability since shippers can scale their volume up or down without worrying about the overhead of fixed-storage capacity.
Cross-docking can be a particularly good option for items that don’t fit within the standardized conveyors, racks and carts used to move most goods — if handled well. In many traditional fulfillment facilities, big and bulky items get relegated to out-of-the-way storage areas using heavily manual processes and special equipment. The extra handling required to manage these items is one reason, among many, that big and bulky merchandise orders often take a long time to reach their recipient.
Cross-docking oversized items eliminates all that, so goods are en route to customers more quickly. The promise of fast delivery can make a big difference in closing a sale.
What cross-docking requires
In an ideal world, all goods could move this way. However, successful cross-docking operations are complex and require solid planning and a skilled operator.
Carefully planned fulfillment facilities and precision scheduling are critical to ensuring goods flow unimpeded. Cross-docking requires a lot of space that must be configured to minimize travel distance and allow smooth movements. Even the number, size and placement of dock doors can make a big impact on efficiency. Combining all of these stringent requirements for a successful cross-docking operation creates a high start-up cost, which makes it cost-prohibitive for many traditional cross-docking providers to set up a national network of cross-docking facilities.
Technology is key to making it all work. It provides visibility into incoming shipments; plans, assigns and executes item movements; and tracks the location of items as they travel. Not every warehouse management system can accommodate this purpose, so cross-docking facilities need software well-tuned to these unique processes.
Robust, real-time data sharing among shippers and cross-docking providers is essential to successful execution. With less inventory in the supply chain, strong forecasting and inventory visibility are important to minimize disruption and ensure shippers can meet demands. Sharing this data with the cross-docking provider as early as possible helps ensure smooth operations.
The level of communication required among the suppliers, the sender, and the cross-docking service provider is substantial. They must work together to synchronize inbound shipments with production schedules and inventory levels and optimize inventory flows. A successful partnership delivers cascading benefits in supplier performance and greater supply chain resilience.
A better way to cross-dock
All that complexity means that when the operation lacks the right focus, technology or expertise, cross-docking won’t deliver on its potential. As with any business relationship, you must make sure the cross-docking provider truly understands the nuances of your business and the products you sell.
Poor collaboration, limited data sharing and misalignment of schedules or processes can lead to delays or misplaced items and hamstring cross-dock efficiency. A cross-docking provider with insufficient labor, processes or technology is often unprepared to meet SLAs, an outcome that quickly shows up in poor end-customer experiences. So it’s vital to thoroughly vet the capabilities, associations, and track record of a potential cross-dock provider. Tour their facilities and show them yours to make sure everyone is aware of the requirements of your goods and customers.
Roadie’s new cross-docking solution, RoadieXD™, doesn’t suffer from these same concerns. As a UPS company, Roadie has access to a nationwide network of state-of-the-art facilities. Combine that with a national network of independent drivers that can deliver up to 100 miles, and many of the challenges and cost concerns associated with traditional cross-docking begin to fade away. Existing Roadie and UPS customers can start using the RoadieXD™ cross-dock network right away.
To learn how you can reduce your inventory carrying costs and improve delivery speeds — even for oversized goods — check out our RoadieXD™ page.
Related Posts
Subscribe to our logistics newsletter
Get once monthly resources and insights into logistics challenges and trends. Add your email in the form to the right, or feel free to jump back into the site!